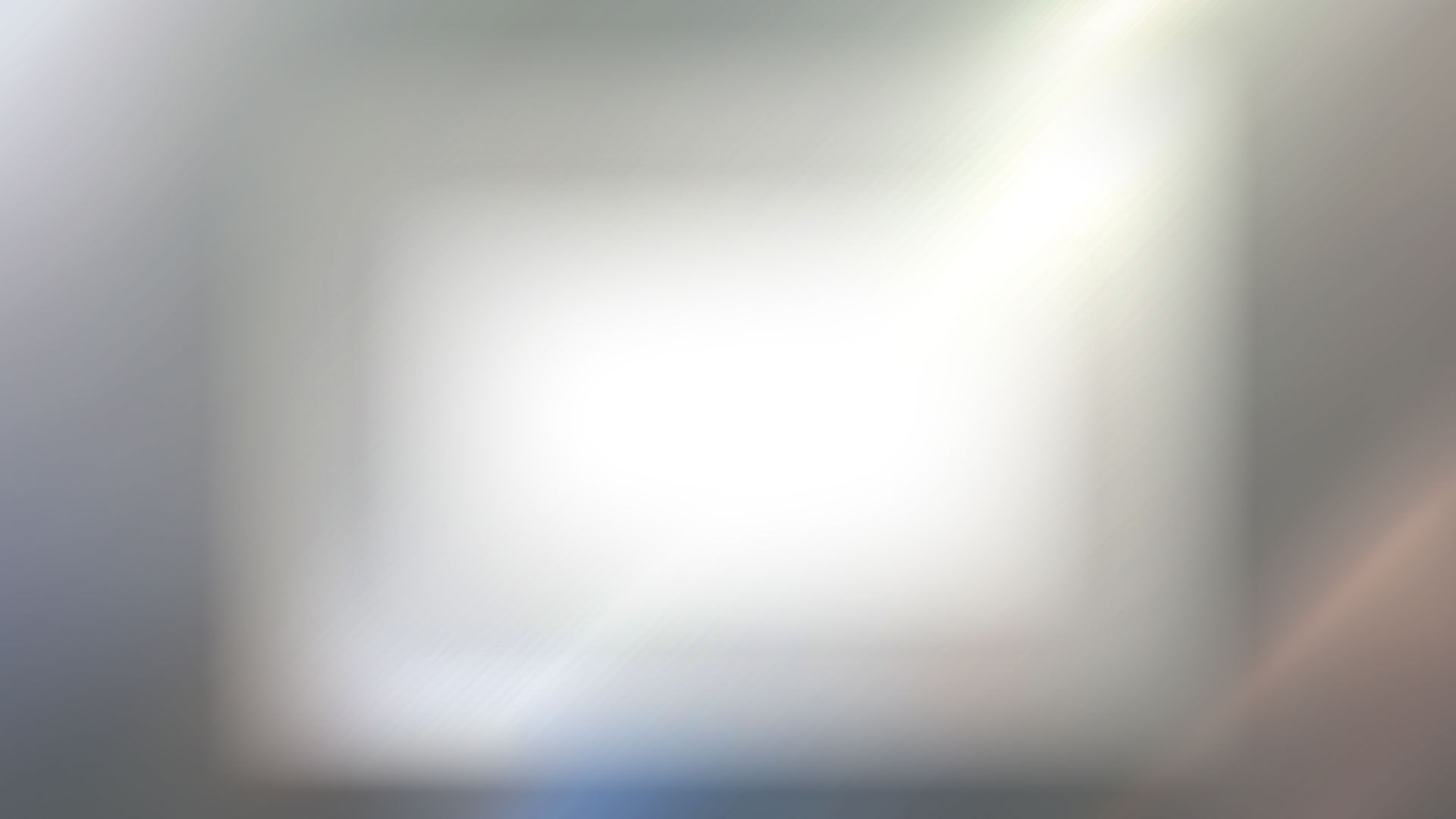


Click Image, Links or Scroll Down for descriptions, standard equipment, options & technical specifications
PLATE ROLLS
Overview:
Plate or Sheet Bending Rolls
fall into 2 general categories, Single or Double Pinch
However they may have different geometries or operational features. Matching the most appropriate machine style to the application is of primary importance to the user in order to maximize the return on investment (ROI).
CLICK LINKS TO GO TO- General Common Roll Styles:
Click Here To Learn More About Making The Right Choice For Your Application
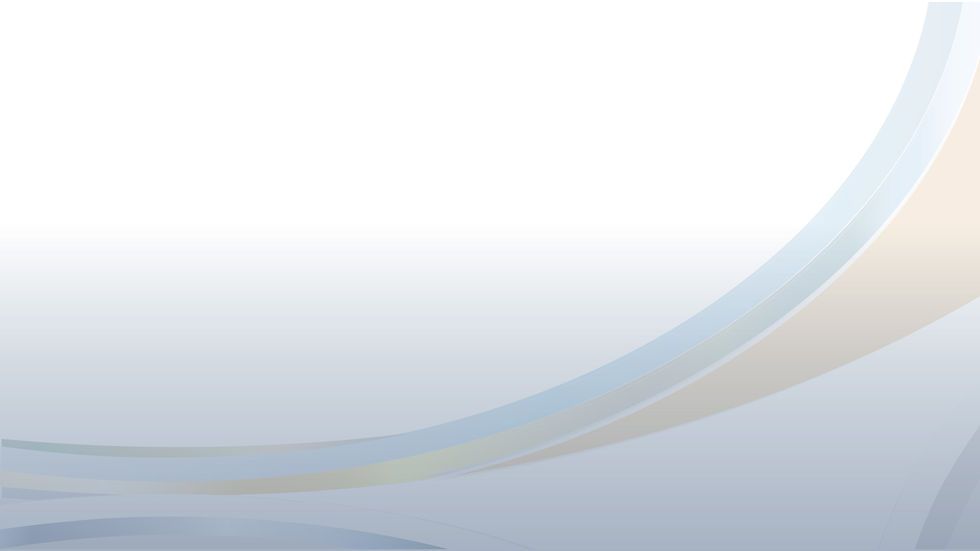
4 Roll Double Pinch Plate Rolls
Manufacturing Range: 1' to 26' Long - 16 GA to 6" thick
(also known as 4 Roll Double Initial Pinch or simply 4 Rolls)
Carell Plate Rolls are built tough for longer machine life and designed to minimize maintenance. Our plate rolls are available in over 60 sizes with capacities from 16 gauge to 6 inches. Carell's range of standard models provides unmatched flexibility and coverage of most any plate rolling requirement. They can be built to handle a wide range of specific rolling requirements that includes shorter or longer lengths from 20 inches to 24 feet, custom roll cambers, slotted rolls for plate with flanges-lips-ribs, patterns for corrugated material, vertical rolling applications and more!

3 Roll Double Initial Pinch Plate Roll
Manufacturing Range 1' to 26' Long - .05" to 6" thick
also known as: 3 Roll Double Initial Pinch
They are available from light to extremely heavy capacities and sometimes referred to as "double pinch pyramid plate rolls’"or "double initial pinch plate rolls". Three roll styles have fixed position top rolls and two offset rollers or "lateral rolls", one on each side and include drop end yokes for easy extraction of the work-piece.Three Roll machines generally require pre-bending the leading end, running the sheet through the machine to pre-bend the trailing end then switching roll rotation direction to roll the cylinder body.
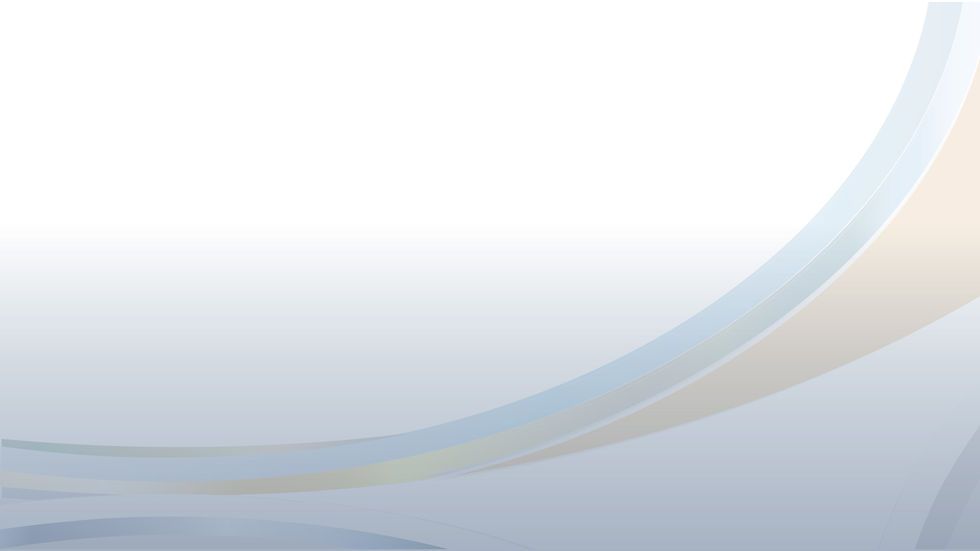
3 Roll Variable Translating Geometry Plate Rolls
Manufacturing Range: 3' to 26' Long - 1/4" to 12" thick
(also known as 3 Roll Variable Translating Geometry)
Variable Translating Geometry Plate Rolls are built for medium, heavy to extremely thick plate applications. The top roll moves up/down and the lower two rolls each move horizontally. This lower roll movement allows increasing the offset distance from the top roll and commensurately increasing mechanical advantage in bending. By adjusting the geometry they can be used similar to single pinch, double pinch and pyramid style machines and require minimal sheet movement during the pre-bend operations.

3 Roll Initial Pinch or Single Initial Pinch Plate Rolls
Initial Pinch-Hydraulic & Mechanical
3' to 12' Long - 1/2" to 26Ga Capacites
(also known as 3 Roll Single Initial Pinch or I.P. Rolls or Slip Rolls)
Initial Pinch or Single Initial Pinch Plate Rolls are generally for lighter capacity applications and may be electro-mechanical or hydraulic. The upper roll is in a fixed position; the lower pinch roll can move up/down to pinch the material. The third roll (the forming roll) is also adjustable. They are cost effective but in contrast may be more labor intensive in a production setting.

Vertical Format Plate Rolls
Vertical Format Plate Rolls can be of nearly any geometry, double pinch, single pinch or pyramid. Vertical rolls are most often used for rolling large diameters and can be advantageous when used in the field for storage tank production. Carell offers automated Vertical Tank Production Systems which are fed from coil stock and can include vertical sheet cutoff and automatic vertical seam welding among other options. These Systems can be used in-house or in the field and increase production output while reducing labor input
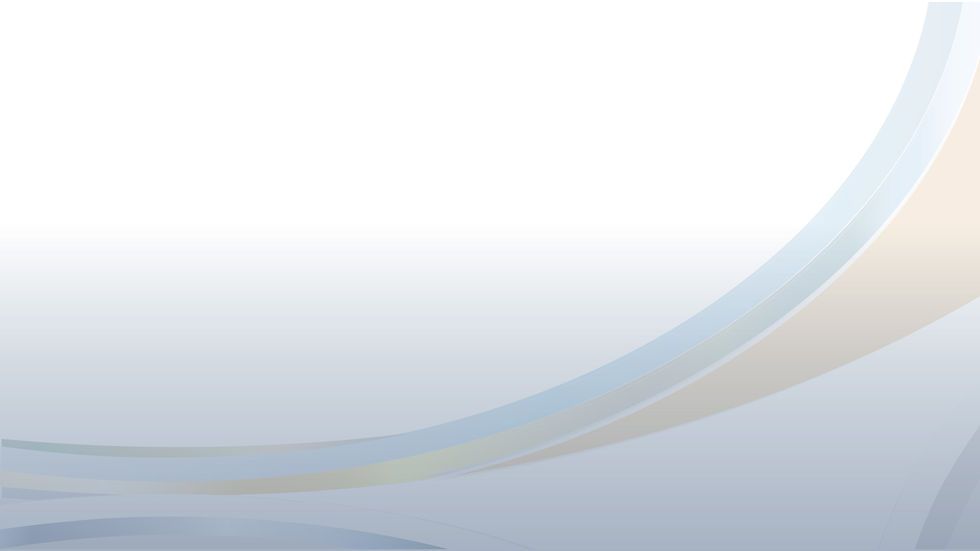
Automatic Cycle & Specialty Plate Rolls
Automatic Cycle Plate Rolls are designed to rapidly produce radiused and cylindrical parts from start to finish at the touch of a button in a cost-effective manner. Machines engineered for high speed continuous production. Easy setup using durable mechanical and electric limit devices. Add an auto loading and ejector system and the Hi-Tech unit becomes a powerful tool reducing part throughput & handling time to an absolute minimumn setting.